「第1回:“モノづくり”の脱炭素化をリードするITプラットフォームの主力工場」はこちら>
先駆的なCFP取得で、CO₂可視化要請にいち早く対応
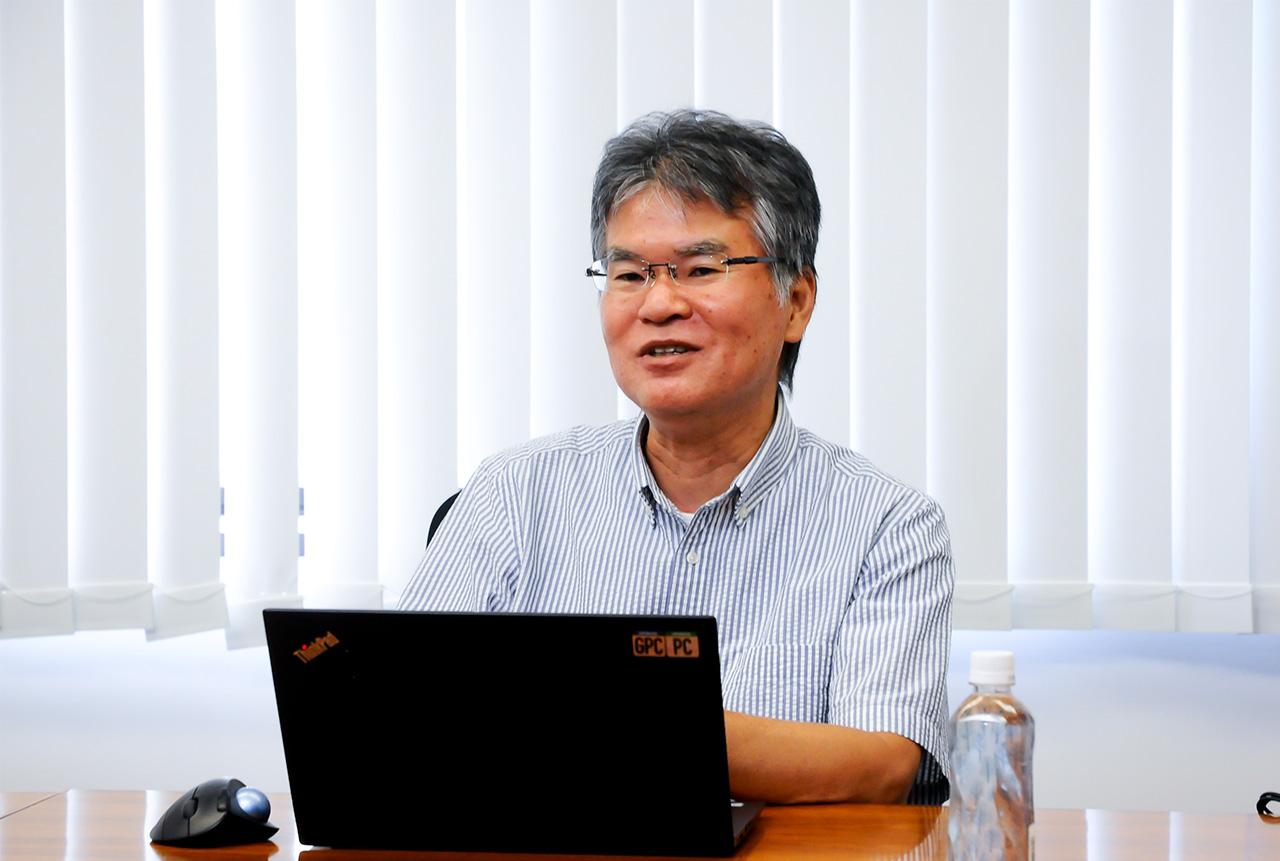
株式会社 日立製作所
ITプロダクツ統括本部 ハードウェア開発本部
プロダクツ第1設計部 第2G
主任技師
古波津 貢
神奈川事業所は現在、製品ライフサイクルを通じたLCA※1ベースのCO₂排出量の算出・可視化実証を推進しています。この実証は、従来お客さまごとの出荷情報をもとに熟練者が手計算で対応していた製品単位のCO₂排出量算出・可視化を、設計部品表(BOM※2)をベースに自動化・システム化するための試みです。2022年度に自社内Scope1、2とバリューチェーンのScope3における上流工程が完了し、現在は2023年度内をめどにScope3の下流を含めた実証を進めています。
同事業所におけるCO₂可視化の取り組みの起点は、経済産業省が2009年から試行事業を開始した「カーボンフットプリント(CFP※3)制度」でした。この制度は、資源採取から生産、使用、廃棄、リサイクルに至る製品のライフサイクル全体を通じて排出された温室効果ガスをCO₂排出量に換算して可視化する仕組みの1つです。「3年間の試行事業の間、日立は神奈川事業所で現在製造しているストレージやサーバー、ネットワークスイッチといった製品のCFP宣言認定を初めて取得し、その後はすべてのストレージ製品でCFP宣言認定を取得・登録しています」と説明するのは、本実証に携わる古波津 貢です。
その後、粛々と進められていたこのCFPの取り組みに、政府による「2050年カーボンニュートラル宣言」が発表された2020年以降、再度スポットライトが当たります。そして近年、欧米諸国からはLCAベースのCO₂排出量の開示が要求され、2024年以降順次導入される欧州エコデザイン規則(ESPR※4)でも、EU域内で販売されるほぼすべての製品にCO₂排出量情報などの付与を義務化。こうして加速するCO₂可視化という時代の要請に、神奈川事業所はいち早く対応してきたのです。
※1 Life Cycle Assessment
※2 Bill of Materials
※3 Carbon Footprint of Products(現在は一般社団法人サステナブル経営推進機構[SuMPO]がSuMPO環境ラベルプログラムとして運営)
※4 Eco-design for Sustainable Products Regulation
精緻なアプローチで正確性と信頼性を追求する実証の現場
CO₂排出量算定プログラムの評価・検証
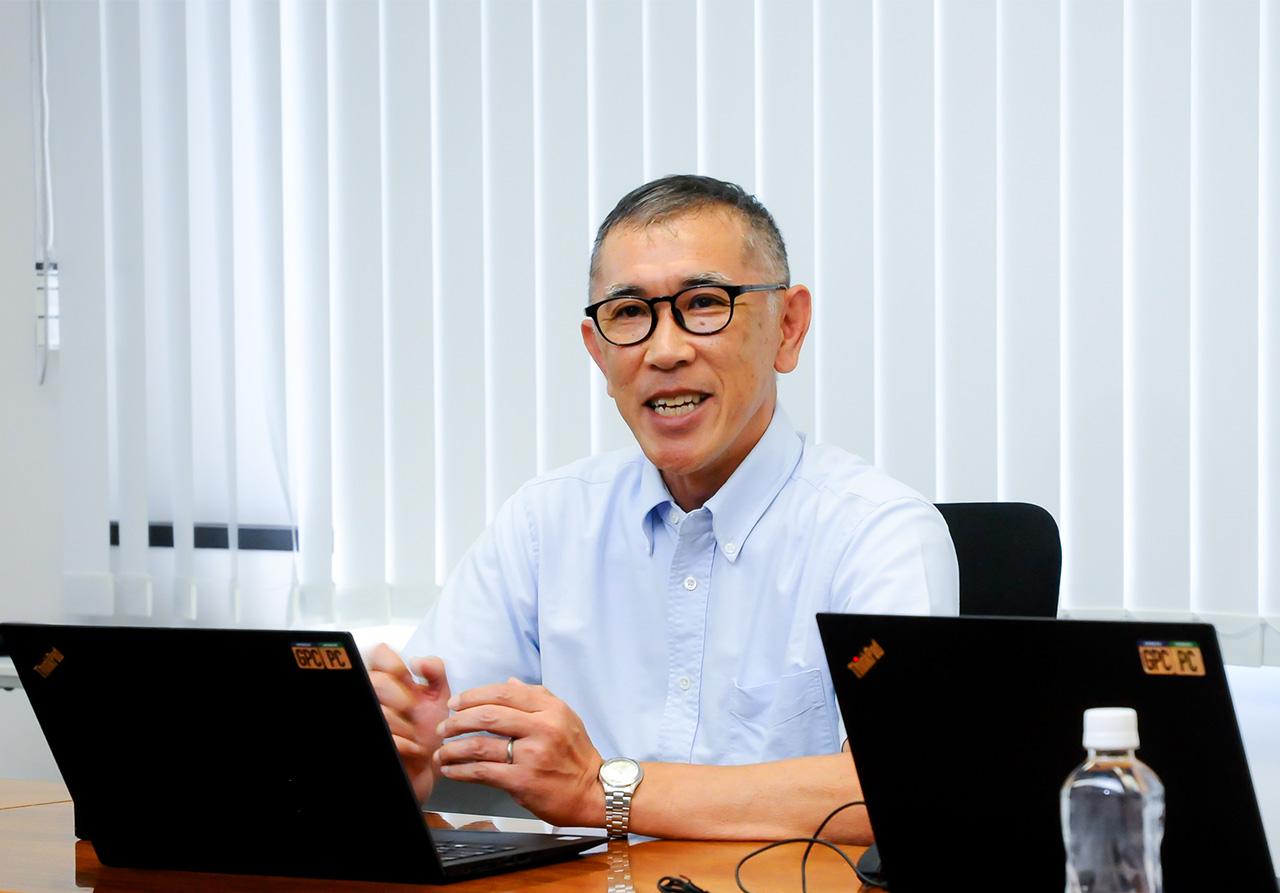
株式会社 日立製作所
ITプロダクツ統括本部 ハードウェア開発本部
プロダクツ第1設計部 第2G
主任技師
西川 秀樹
本実証で取り組んでいるのが、主に消費電力などのデータ集計ノウハウの確立と、集計データに基づくCO₂排出量算定プログラムのための要件定義、さらにそのプログラムの評価・検証です。これまで神奈川事業所では、製品の設計者が各所から種々の情報を集めてExcelに取り込み、自らCO₂排出量を算出していました。今回の実証では、こうした経験のなかで培われた「どこからどのような情報を集め、どのように計算するか」といったノウハウのプログラム化を進めています。
この仕事を担う西川 秀樹は、「主にツールの計算結果と従来の手計算で出した数値にかい離がないかといった点を検証していますが、あちこちに散らばっている設計情報を集めるのはとても骨の折れる作業でした」とその難しさを語ります。実際、製品は多数の部品から構成されますが、その部品表は階層構造になっており、各素材も鉄やアルミ、銅、ポリカーボネイト、ABSなど多岐にわたります。また、部品ごとにCO₂排出量の算出基準となる原単位が異なるほか、あるシステムでは「001」と登録されている部品が、別のシステムでは「1」と記載されるなど、その突合すら容易ではありませんでしたが、長年培われた経験知がそうした困難を克服する力になったと言います。
Scope1、2:製造時におけるCO₂排出量の算出・可視化
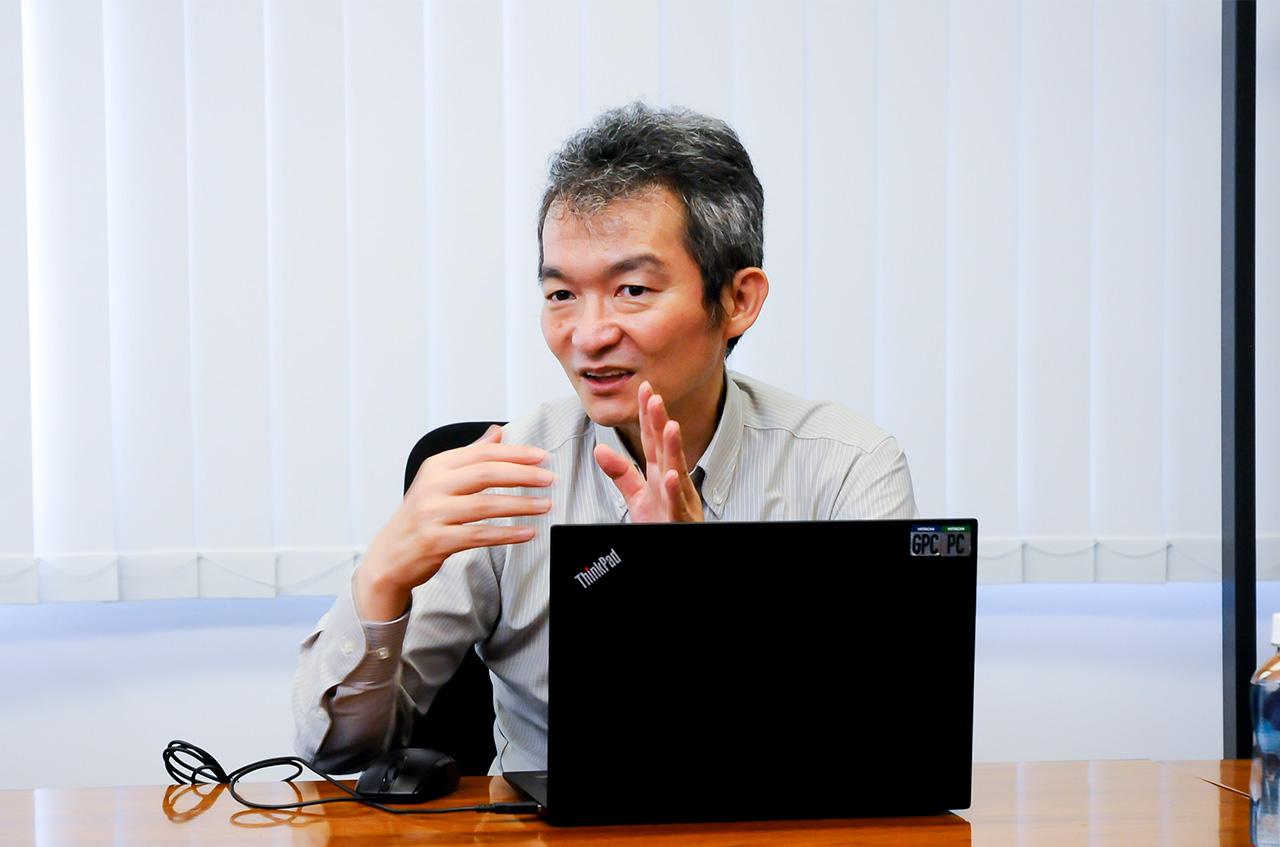
株式会社 日立製作所
ITプロダクツ統括本部 グローバルサプライチェーン本部
サプライチェーン改革推進部
担当部長
長瀬 則和
製品製造時に使う電力のうち、その約9割は組み立て工程ではなく、完成品の動作や耐久性などをチェックする装置検査工程で消費されます。検査工程では、絶縁耐圧試験や機能試験、エージング試験、ヒートラン試験が実施されますが、こうした試験用設備・システムで実際に使われている消費電力を工場構内の配電盤から計測。生産ラインに影響を与えることなく、これを個々の製品モデル単位で実測しています。
「多数の装置が稼働する工場の電力系統はとても複雑で、計測対象の装置とは別系統の配電盤から数値を取っていたこともありました。また、エージング試験などでテスト装置の内部に格納する製品の台数次第で1台当たりの消費電力は変わってきてしまうため、実際の生産計画に照らしながら、製造される製品ごとの消費電力を正確に計測することが重要です」と担当者である長瀬 則和は振り返ります。
Scope3:製品使用時におけるCO₂ 排出量の算出・可視化
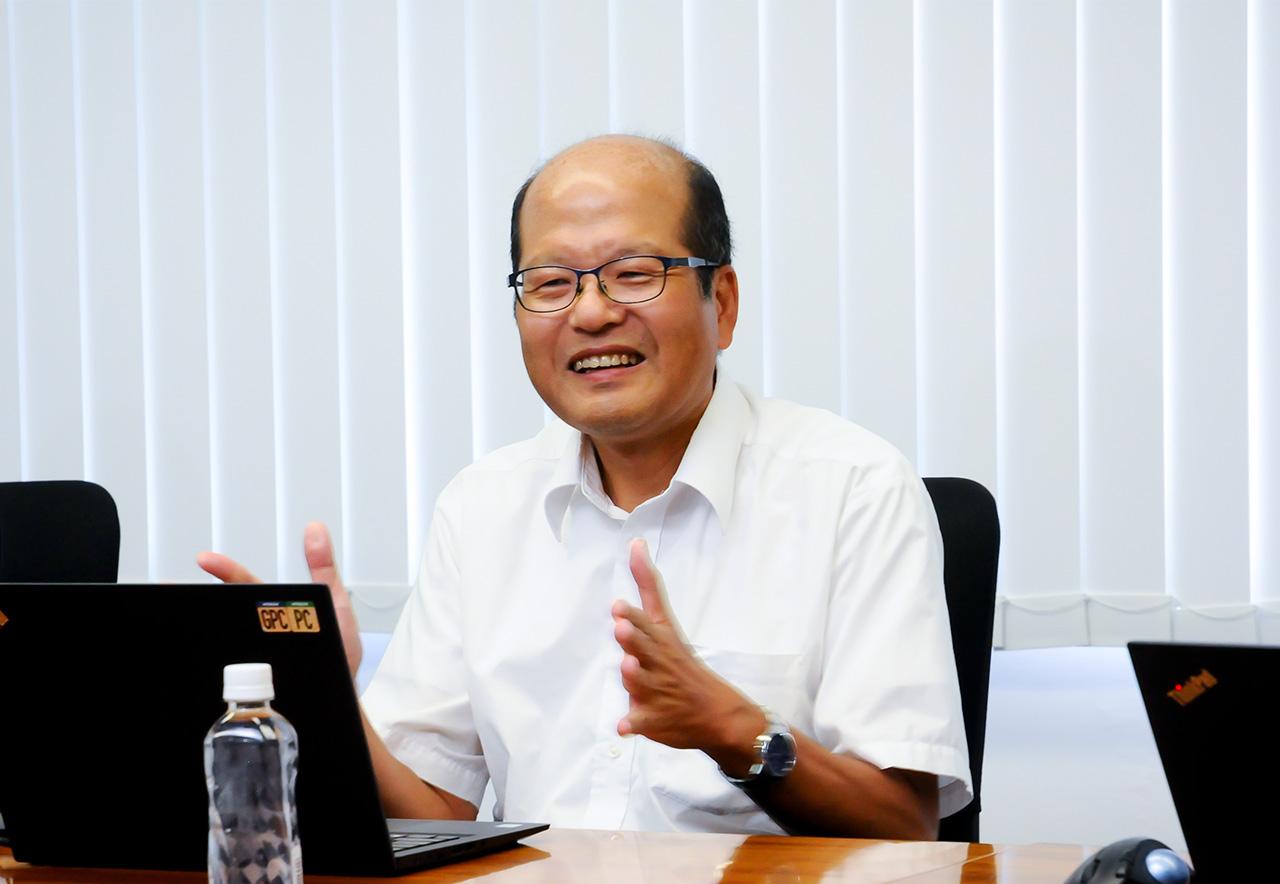
株式会社 日立製作所
ITプロダクツ統括本部 ハードウェア開発本部
プロダクツ第1設計部 第2G
主任技師
堀 雅則
ストレージ製品の場合、製造時に生じるCO₂は製品ライフサイクル全体の5%程度に過ぎず、残りの95%が製品使用時に排出されます。神奈川事業所では、新製品を開発するたびに、使用時の消費電力を測定していますが、その際、お客さまの使い方やハードウェア構成をパターン化し、それぞれの消費電力量の最大値を算出してきました。
測定を担当する堀 雅則は、「ストレージの消費電力はランダム/シーケンシャルといったアクセスパターン、さらにリード/ライト、読み書きするデータの長さ、ディスク径や構成台数によって異なります。そのため、各製品の最大消費電力を提示するには、これらの与件を組み合わせた多数のパターンを1つずつ計測する必要がありました」と説明。こうしたきめ細やかで丁寧な取り組みが、本実証の正確性と信頼性を支えているのです。
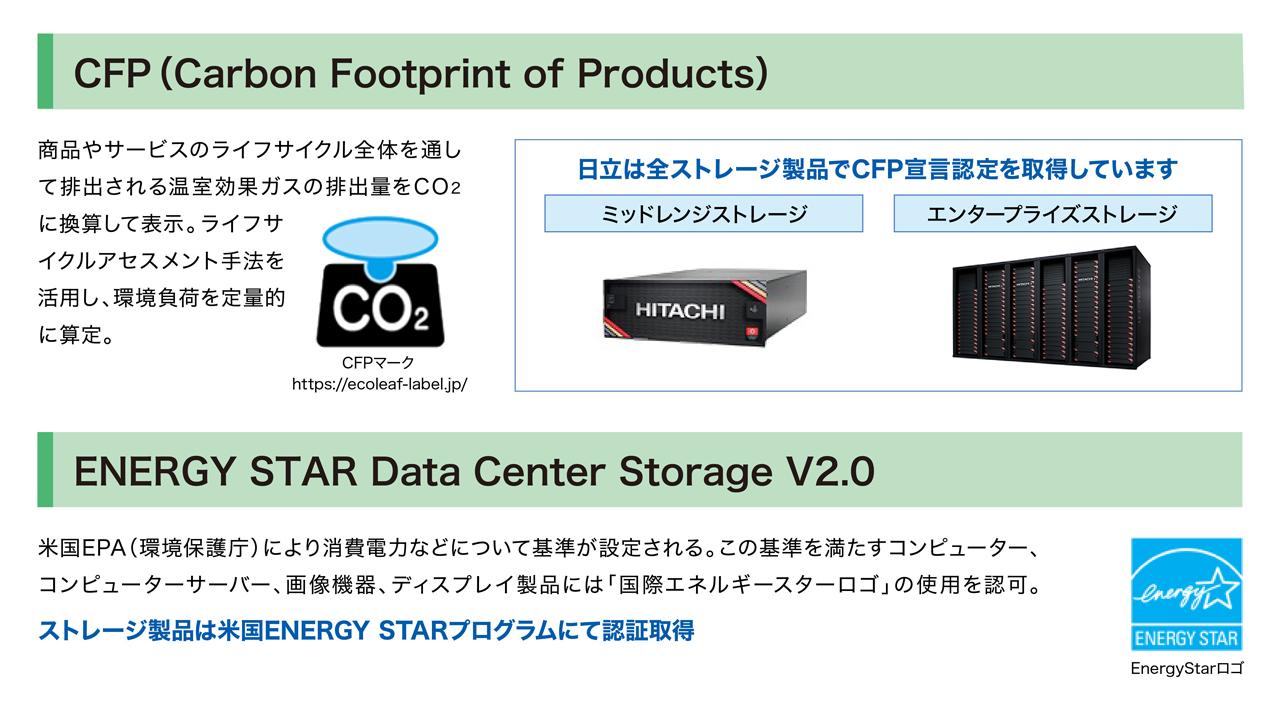
さまざまな認証を取得し排出量の見える化と省エネ化を推進しているストレージ製品
脱炭素社会実現に向けたCO₂排出量算出・可視化というスタートライン
例えば、CDPという英国の慈善団体が管理するNGOを経由して、製品のユーザー企業がサプライヤー側に環境情報の開示を要請するなど、欧米が先導するLCAベースのCO₂排出量に関する情報開示要求は、近年さらに強まっています。こうした動向に鑑みても、従来人手に頼っていたCO₂排出量算出の自動化をめざす本実証の意義は大きく、神奈川事業所では今後より高度化していく要求に応じて算出精度の向上にも注力していく方針です。
「必要なのは、お客さまが把握できたCO₂排出量をどうすれば減らしていけるか、それを支援する製品やサービスなのです」と、古波津は脱炭素化へ向けたこれからを見据えます。そういう意味で、今回の実証がめざすCO₂排出量の算出・可視化は「ゴール」ではなく、あくまでも「スタート」。ここを起点に、環境に配慮した製品やサービスの提供を通じてお客さまの環境ニーズに応えながら、日立は今後も脱炭素社会の実現を果敢に追求していきます。
「第3回:脱炭素化の次元を変える、飽くなき探求と精緻な実証の結実」はこちら>
他社登録商標
・Excelは、米国Microsoft Corporationの米国およびその他の国における登録商標または商標です。
・その他、本記事に記載の会社名、商品名、製品名は、それぞれの会社の商標または登録商標です。