「第1回:『デジタル化』とは、何をすることか。」はこちら>
「第2回:人間とコンピュータの間を埋めてきた『レイヤー構造』。」はこちら>
「第3回:DXは『抽象化』から始まる。」はこちら>
DXがたもたらすのは、UX。
近年、「モノからコトへ」という言葉をよく聞きます。そのめざすところは、プロダクトの機能や性能に価値を見出すという従来の製造業ではなく、消費者にとって価値のある経験を創出するというものでしょう。「コト」づくりビジネスに舵を切るために、「データをいかに活用するか」という点も強調されます。しかし、自社の製品同士をデータ連携させるだけでは価値を生み出せません。より大事なのは、ユーザーとの間でデータ連携すること。つまり、ユーザーは「製品を買って使っている」と考えるのではなく、「ユーザーの脳が製品とデータをやりとりしながら、一緒になってデータ処理をしている」と考えることです。
スマートフォンで地図アプリを使っているシーンを想像してみてください。ユーザーはアプリに行きたい場所を入力し、表示されたルートをたどって目的地をめざします。このプロセスを可能にするのが地図アプリの役割です。しかし、地図アプリの矢印に合わせるように身体をコントロールしているのはもちろん人間の脳ですよね。ユーザーが目的地に到着するというプロセスがうまく実行されるように、脳と地図アプリがデータをやりとりして連携・協働しているわけです。このようにユーザーの脳と一緒にプロセスを作り上げて、全体をスムーズにする、また、脳とアプリとの間で適切な役割分担を新たに行うというのが、コトを考える出発点です。
あるいは、エクササイズをするとき、わたしたちは「次はこのエクササイズをやろう」「これ以上続けるとやりすぎだから、この辺でやめておこう」といった意思決定をしてから動作をしています。そのプロセスを助けることは、ユーザーが「運動不足を解消して、健康長寿をめざす」という価値につながるはずです。このように、ユーザーの脳と製品・サービスとがコラボ、すなわちデータ連携し、ユーザーにとっての価値を生むのが「モノからコト」への本質です。
これがコトづくりを通じてユーザーに価値を提供するということなのです。言い換えると、UX(User eXperience)。
日系企業にありがちなのは、製品を開発するときにUXをなかなか意識できないことです。あくまでも、「モノ」をどう作るかを起点に考えてしまう。そうではなく、一歩引いて、「ユーザーとともに経験を作っていて、その手段としてたまたまモノが使われる」という考え方。つまり、消費者の行動を含めた一連のプロセスとして全体をまず捉えて、その後でモノを位置づける。ここでも、物事を抽象化して捉える発想がデジタルには不可欠なのです。
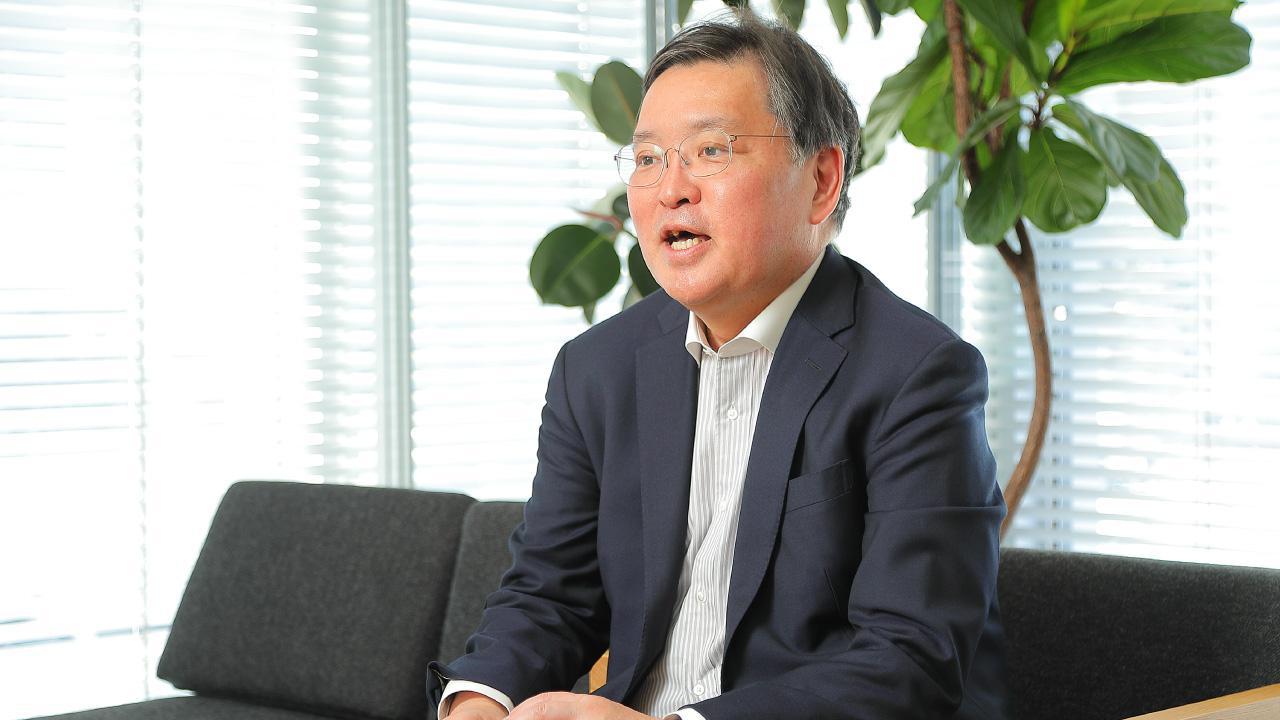
日本のDXの先駆、ダイセルの生産革新
日本で「モノからコトへ」へのシフトがなかなか進まないのはなぜか。わたしは、「産業=バリューチェーン」という見方にも原因があるのではないかと考えています。ここで言うバリューチェーンとは、原材料を加工し、中間製品を経て、完成品が出来上がるという製造の工程で、それが産業全体を表現しているという考え方です。
そうではない見方に至るために紹介するのが、ダイセルという会社が行ってきた生産革新の取り組みです。スマートフォンなどのディスプレイの保護フィルムやエアバッグ用のインフレータ(ガス発生装置)をはじめとする化学製品を生産している会社です。今から20年ほど前、ダイセルは円高による国内工場のコスト競争力の低下に悩んでいました。同時に、団塊の世代の熟練技術者の大量定年退職が近づきつつありました。当時の多くの製造業も同じ課題に直面していたと思います。
ダイセルがまず行ったのは、熟練技術者のノウハウ・暗黙知を徹底して引き出し、数十万に及ぶ「ケース」にすることでした。それと併せて、組織内の情報のやりとりの見える化や、センサー情報の表示方法の見直しを行いました。そのうえで、最終的には設備が行う製造プロセスそのものも見直しました。ダイセルの一連の取り組みをわたしなりに要約すれば、すべてを「プロセス」として同じ土俵に乗せて考える、ということになります。
その元をたどれば、5つになります。1つめが、各製造ラインで配管や蒸留塔などの「機械設備」が行う反応プロセス。2つめが、プラントの中を通る管の温度や圧力を測る「センサー」を使って状態を把握しディスプレイに表示するプロセス。3つめは、センサーが感知した状態に応じてプラントをどう制御するか判断する際の根拠となる、個々のエンジニアの「暗黙知」。それでも判断できない場合に、組織内で状況を共有することで知見を結集させる、4つめの「組織知」。そして、それらをサポートする「IT」です。
ポイントは、ダイセルはこの5つを区別せずに、一旦すべてを俎板(まないた)の上に乗せたということです。設備が担おうが、熟練技術者が担おうが、それらがすべて組み合わさってビジネスがあるのだから、「全体をどう最適化するか」という視点から境目なく考えようという発想です。そのうえで、可能な限りプロセスの処理をソフトウェアに移しました。工場のハードウェアはそのままに、オペレーションシステムであるソフトウェアを再構築したのです。そして、熟練技術者ではなくともプラントの運転を可能にしただけでなく、製造原価を約20%も削減することに成功しました。
ダイセルが起こしたもう1つの革新
要するにダイセルは、化学プラントの内部で起きていること、個々の技術者がやっていること、組織がやっていることを抽象化し、構造化してプロセスだけ取り出したわけです。
それを踏まえて、自社が行った生産革新の手法をITソリューションとして他社に販売しました。そこまで抽象化すると、基礎的な動作・プロセスは、例えばガラスでも鉄鋼でも化学でも同じになるからです。第3回でお話ししたIntelの例を彷彿とさせるエピソードです。
冒頭で、DXがUXをもたらすと言いましたが、それはダイセルの例にも当てはまります。ダイセルは、プラントの運転に当たる技術者をプラントやシステムのユーザーだと捉えました。生産革新によって、経験の浅い技術者でも過大な負荷なくオペレーションを担い、新たな価値創造を追求できるというUXをもたらしたのが、ダイセルの成し遂げたことです。
「第5回:ソフトウェアの秩序が、組織を規定する。」はこちら>
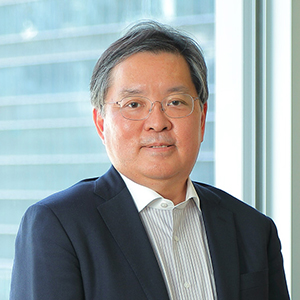
西山圭太(にしやま けいた)
東京大学未来ビジョン研究センター 客員教授
株式会社経営共創基盤 シニア・エグゼクティブ・フェロー
1963年東京都生まれ。1985年東京大学法学部卒業後、通商産業省入省。1992年オックスフォード大学哲学・政治学・経済学コース修了。株式会社産業革新機構専務執行役員、東京電力経営財務調査タスクフォース事務局長、経済産業省大臣官房審議官(経済産業政策局担当)、東京電力ホールディングス株式会社取締役、経済産業省商務情報政策局長などを歴任。日本の経済・産業システムの第一線で活躍したのち、2020年夏に退官。著書に『DXの思考法』(文藝春秋)。