※1 huMan(人)/ Machine(設備)/ Material(モノ)/ Method(方法)
循環システムと成熟度モデルで工場を進化させる
大みか事業所の大きな特長となっている「高効率生産モデル」は、生産現場の「人・モノ・設備」の状態や動きをRFIDやカメラ映像などによって可視化し、既存のITシステムとつないで、分析・シミュレーションを行うことで解決策を立案します。その過程では「Sense(収集)」→「Think(分析)」→「Act(対策)」による循環システムを確立し、モノづくり現場の継続的な改善に取り組んでいきます。
生産システムの生産性や品質を判断する基準として、独自の「成熟度モデル」を定義しています。対象となる工程が「見える」「つなげる」「流れを制御する」「問題を把握・対策する」「将来を予見する」「連携と協調」という6つのレベルの、どこに当てはまるか、どう進化させていくかを常に見極めながら、循環システムを活用してレベルアップしていくアプローチにより、生産現場の全体最適化を追求しているのです。
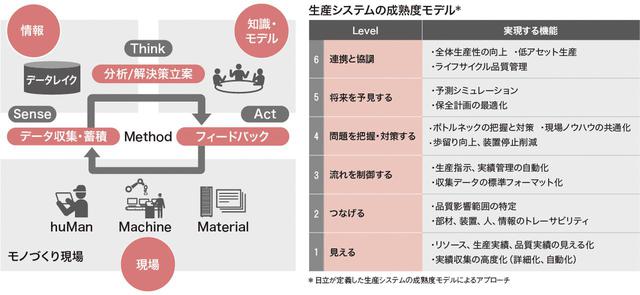
循環システムと成熟度モデルによるアプローチ
制御盤組み立てラインの生産リードタイムを50%削減
では、この高効率生産モデルが、大みか事業所の生産システムをどのように進化させていったのかを、具体的に説明します。
例えば、情報制御システムの心臓部である制御盤の組み立てラインで生産される制御盤は多くの場合、用途ごとにカスタマイズされた一品生産となり、板金加工や組み立てといった複雑な工程で構成されています。そのため従来は、「作業者のスキルによって工程進捗(しんちょく)や品質に影響が生じる」「納期変更などがあると部材が滞留する」などの課題を抱えていました。
そこでこの課題解決に向け、約8万枚のRFIDタグと約450台のRFIDリーダー、作業者の動きをとらえる作業分析カメラなどを使い、「誰が」「いつ」「どこで」「何の」作業をしているのかという情報をリアルタイムに収集。工程管理システムや生産管理システムなど、既存のシステムが蓄積するさまざまな情報もあわせて共有し、生産現場全体の人とモノの動態をリアルタイムに俯瞰(ふかん)できる仕組みを構築しました。
これにより、各作業の負荷バランスを現場リーダーが把握することができ、人員を含めた生産リソースの適正配置を行うことで、生産計画の順守に向けたタイムリーな対応を進めることが可能となりました。
こうしたデータの収集・分析・現場へのフィードバックという循環サイクルをIoTシステムで加速することで、生産リードタイムを50%短縮。さらに、計画立案から設計、製造までを最適化することにより、需要変動や急な仕様変更への迅速な対応に加え、適切な部品納期を提示することで発注時期を調節。棚卸し資産の縮減にも貢献しています。
多品種少量生産のプリント基板生産ラインを高効率化
もう1つの事例がプリント基板の生産ラインです。プリント基板は発電所や工場などの制御システムの中核となる製品で、産業用コンピューターなどにも使用されています。その自動加工生産現場では従来、「計画と実績のかい離が即座に把握できない」「設備異常による突然の故障・停止が発生する」「部品の入出庫に手間がかかり、在庫にも過不足が生じる」などの課題がありました。
これらの課題を解決するため、大みか事業所では各種設備からデータ収集、生産計画・実績や設備の稼働状況を可視化する仕組みを構築。稼働実績の分析結果などをすばやく生産計画にフィードバックすることで、タクトバランスが改善され、生産性も大きく向上。設備異常に関しても、稼働状況や使用頻度を常時監視することで、保守・メンテナンスの時期を把握できるようになりました。
部品供給/在庫の適正化については、電子部品用自動倉庫と自動搬送装置(AGV)を導入。倉庫・ライン内の在庫状況を部品単位で正確に把握することで、常に適正な数量の部品を自動供給する仕組みを整えました。生産の前工程にも自動倉庫とAGVを導入し、部品入出庫の作業を自動化したほか、設備からリアルタイムに収集した実績・稼働データを使い、ライン全体の生産最適化を実現しました。
培った知見を広くお客さまへ
大みか事業所で培った高効率生産モデルは、Lumada(※2)のソリューションコアとして、お客さま企業にも幅広く提供されています。例えば、プリント基板生産ラインの高効率生産モデルは、JUKI株式会社との協創で変種変量生産を最適化する「プリント基板生産最適化ソリューション」として外販を行っており、JUKIのグループ会社であるJUKI産機テクノロジー株式会社では、およそ30%の生産性向上という成果を上げています。
日立は製造業のお客さま向けに、それぞれの課題やIoT化のレベルに合わせ、データの活用方法を一緒に考え、導入から課題解決までをワンストップでサポートするソリューションも提供しています。これからも大みか事業所で培った知見を生かし、生産現場の可視化や、知識の属人性からの脱却、形式知を活用した品質・生産効率の向上など、お客さまのモノづくり現場のデジタル化とデジタルトランスフォーメーション(DX)を継続的に支援していきます。
※2 お客さまのデータから価値を創出し、デジタルイノベーションを加速するための、日立の先進的なデジタル技術を活用したソリューション・サービス・テクノロジーの総称
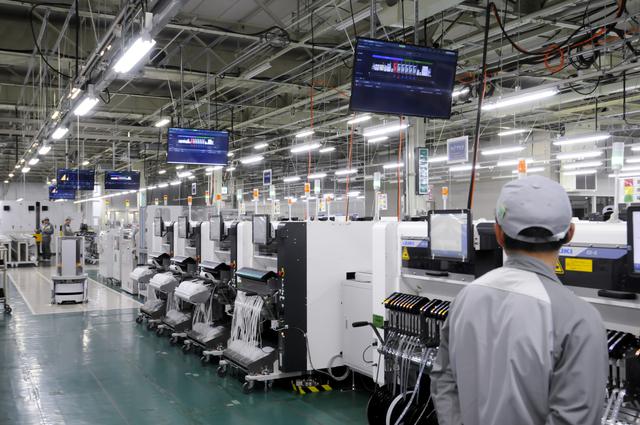
第3回 「全体システムを止めない『自律分散フレームワーク』」はこちら>>
関連記事
他社登録商標
本誌記載の会社名、商品名、製品名は、それぞれの会社の商標または登録商標です。